Industrial coatings ensure protection against mechanical, chemical and environmental degradation. Different types of coatings have different physical and chemical properties. Some are corrosion resistant, whereas some perform when exposed to UV. Being familiar with which applications they are most appropriate for will help you get the highest level of protection and the best finish to your property all the time. Let’s explore the common types of industrial coatings to choose the ideal one.
Epoxy coatings
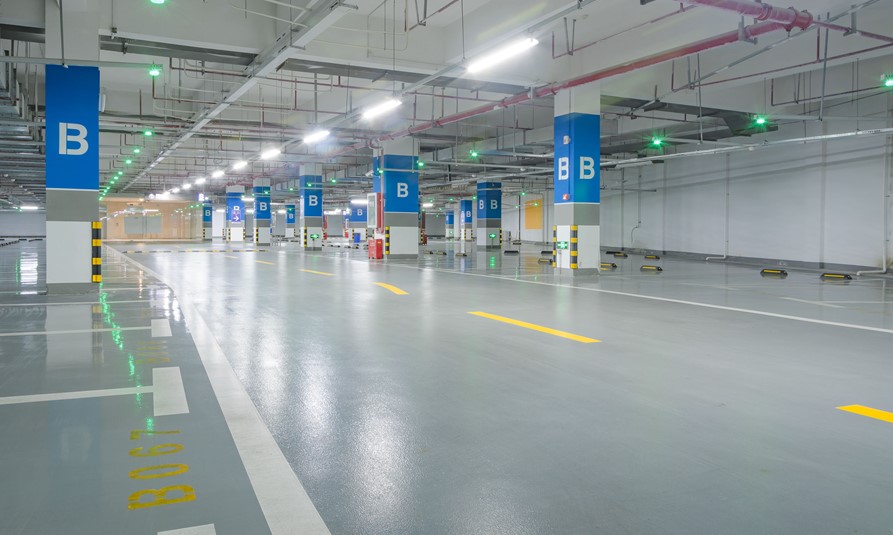
Image by evening_tao on Freepik
This type of coating typically consists of an epoxy base and curing agent. You can achieve a wide range of coating properties by mixing these two ingredients in distinct ratios: epoxy mastic coatings offer outstanding film thickness, epoxy polyamide coatings offer good moisture resistance, and phenolic epoxy coatings offer great chemical resistance.
Due to versatility, they can meet all the project demands as a primer, intermediate coat or topcoat. Epoxy coatings are highly effective against high temperatures up to 1400 degrees Fahrenheit. They are long-lasting, waterproof and shock-resistant.
Epoxies also effectively resist abrasion, corrosion and weathering. They can increase visibility with high sheen and reflective light sources. One notable drawback of this coating is that it chalks when exposed to sunlight. This is why epoxy coatings are mostly used in interior or submerged applications. Quality epoxy floor coatings for indoor concrete floors work as the best concrete sealing. They are also low in flexibility.
Polysiloxane coatings
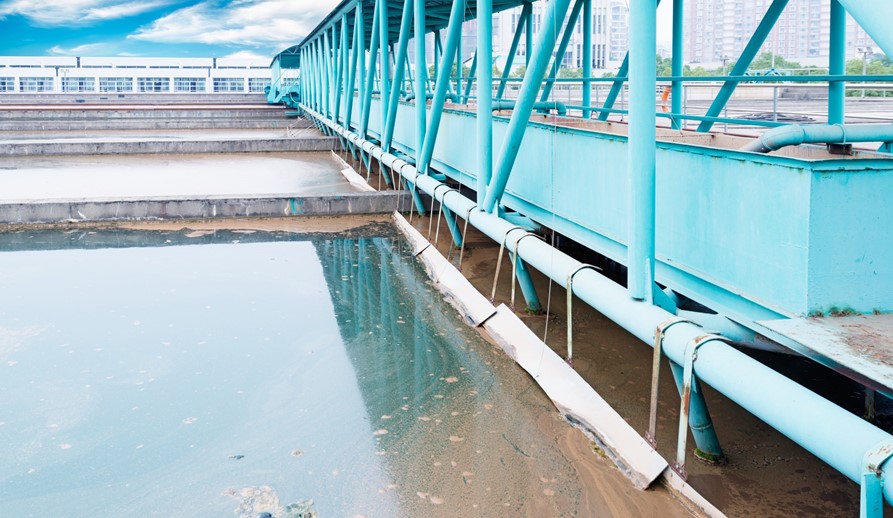
Polysiloxanes are comparatively a new addition to the market. These coating systems provide weather resistance and excellent abrasion. They have appearance retention benefits as well. However, polysiloxanes fail to provide flexibility and corrosion resistance.
You can formulate epoxy polysiloxane coatings, combining the benefits of polysiloxanes with epoxies. They provide weather, UV, chemical and corrosion resistance and industry-leading abrasion. They work well even in high temperatures. Epoxy polysiloxane hybrid coatings cost more than epoxies and polyurethanes. But they can be applied more quickly and last longer, providing long-term value for many applications.
This coating can be used in a wide range of industrial applications, including wastewater treatment plants, highway bridges, marine structures, storage tanks or anywhere that needs a long-lasting, high-performing coating system.
Polyurethane coatings
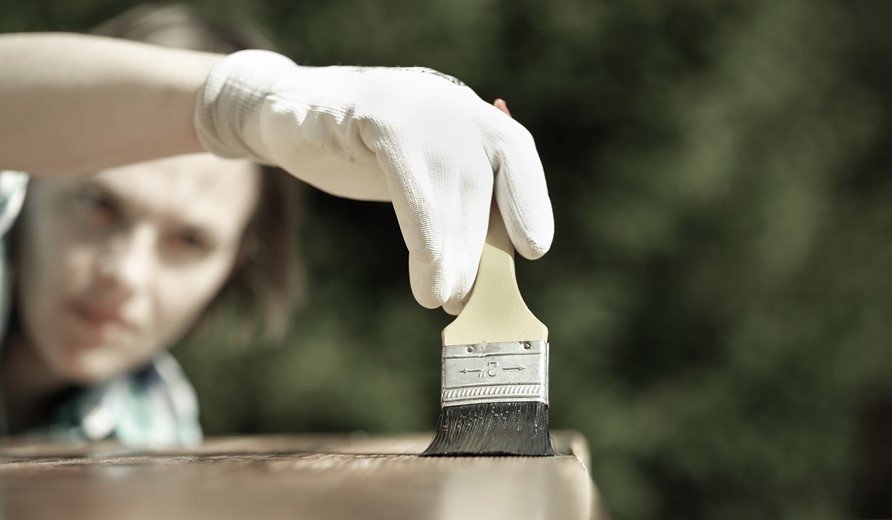
Polyurethane coatings are durable. They are flexible and don’t crack or flake. They are also highly resistant to chemicals, extreme temperatures and water. The abrasion-resistant, high-gloss colour retention finish makes them ideal to use as a topcoat for surfaces to remain scratch-free and smooth.
You can apply polyurethane as a protection for other coatings. For instance, epoxy intermediate coat and topcoat above zinc-rich primer. They are considered the most versatile coating after epoxies. They can even be used as a topcoat on floors, highways, concrete walls, nuclear plants, large ships, etc. These coatings have two categories: aromatic and aliphatic.
- Aromatic polyurethane coatings form a white film and tend to weaken when exposed to sunlight and air. But they perform best for surfaces in submerged environments.
- Aliphatic polyurethane coatings can withstand ultraviolet rays. They can retain colour even following prolonged exposure to sunlight. These characteristics make them ideal for outdoor applications.
The downside of polyurethane is that it is higher priced than epoxies. They also contain harmful chemicals. Some chemicals used as byproducts of polyurethane production are Isocyanates, toluene, phosgene, diamines, ozone-depleting gasses, and halogenated flame retardants. That is why, as a general precaution, workers must wear protective gear when applying polyurethanes.
Zinc-rich coatings
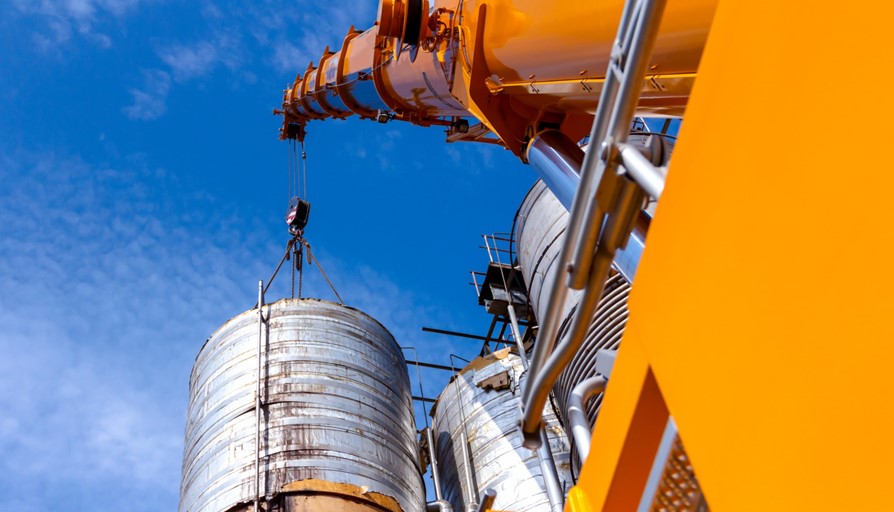
These coatings offer galvanic protection, particularly on steel surfaces. They are corrosion and abrasion-resistant. When exposed to the environment, the particles corrode before the steel surface does. As the zinc dust breaks down, it creates a protection barrier on steel to resist environmental elements.
They received their classification due to the variation in zinc dust in their formulation. Zinc-rich coatings come in two types: organic and inorganic.
- Organic zinc-rich coatings contain epoxy or polyurethane binders
- Inorganic zinc-rich coatings contain silicate binders
Both coatings are highly durable, but they are vulnerable to alkaline substances and acids. This is why they are mostly used as primers in a two-coat or three-coat system before applying a more long-lasting coating as a topcoat. They are often used on surfaces in environments that are subjected to significant levels of corrosion, such as bridges.
Silicone coatings
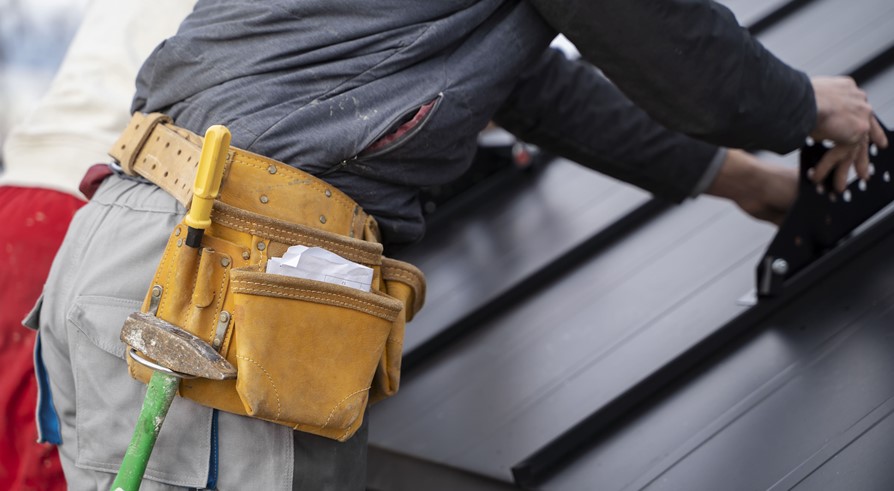
Image by Freepik
These costings are excellent in flexibility and weather resistance. They are mostly used in applications where protection against high temperatures is required, for instance, on furnace linings and high-temperature gaskets. Silicon coatings can resist harmful ultraviolet rays.
They can even reflect the sunlight up to 80%-90%. They don’t chalk, crack or degrade from prolonged exposure to sunlight. These characteristics made them an ideal choice for outdoor applications like roofs. On the downside, these coatings attract dirt and airborne dust particles easily. They are challenging to apply and get slippery when wet.
Acrylic Coatings

Image by Freepik
These types of coating have quick drying capability and long-lasting colour retention properties. They offer a high-gloss finish. These make acrylic coatings the perfect choice for exterior surfaces. The acrylic coating is used in different formulations such as waterborne, powder, and solvent-borne. By changing the ratio of binders and additives, you can achieve ideal coatings to meet your specific needs.
They are cost-effective and easy to work with. Even these coatings are used as a primer due to their ability to better adhere to other coatings on surfaces. Acrylic coatings are popular in the automotive industry due to their corrosion protection characteristic. However, they do not perform well with water and must be applied at 50°F temperature or higher.
Ceramic coatings
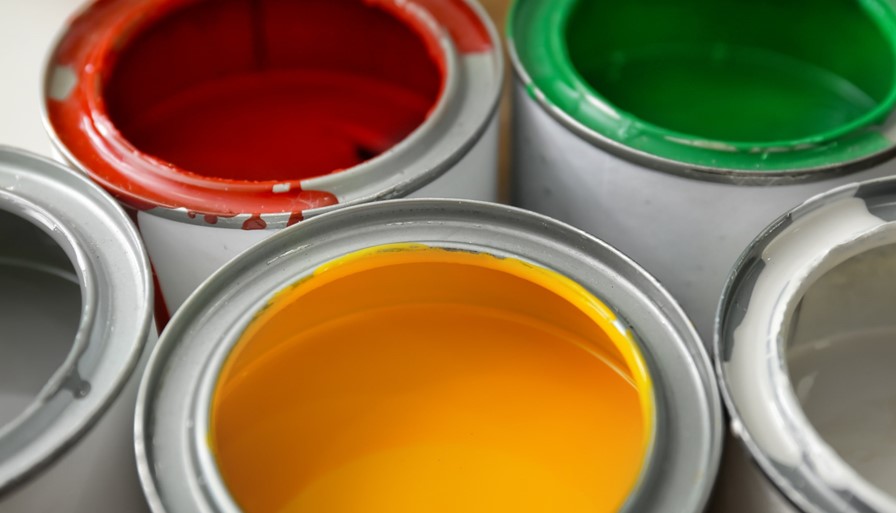
In addition to improved durability and corrosion protection, ceramic paint coatings have unique characteristics. They are superior thermal insulation and have both chemical and dimensional stability. In industrial coatings projects, ceramic polymer can protect piping systems and tanks against UV radiation, water, chemicals, moisture, and high operating temperatures. But, these coatings should never be applied to surfaces exposed to compressive stress or tensile. Plastic deformation can lead to fracture, compromising the integrity of the ceramic coating.
Alkyd coatings
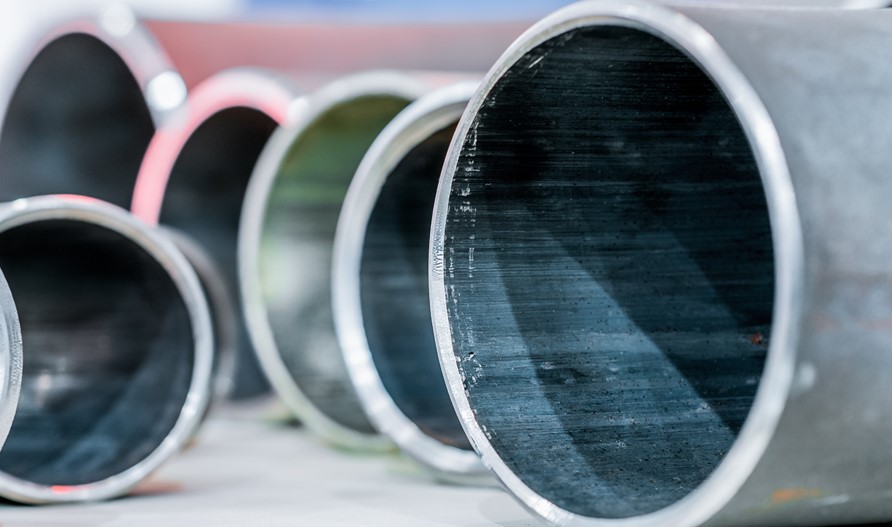
“alkyd” is a term that comes from the words “alcohol” and “acid.” It describes the resin’s origin from which the coating derives its film-forming capabilities. Although alkyds are not as durable as epoxy and polyurethane coatings, they are strong and damage-resistant, especially against wear and tear.
These coatings are also moisture-resistant and produce an attractive glossy finish. They can be used for both interior and exterior surfaces, including underwater and underground assets. You can create a custom alkyd coating, adjusting ingredients as per specific conditions. One of the notable problems is it takes a longer time to dry.
Polyester Coatings
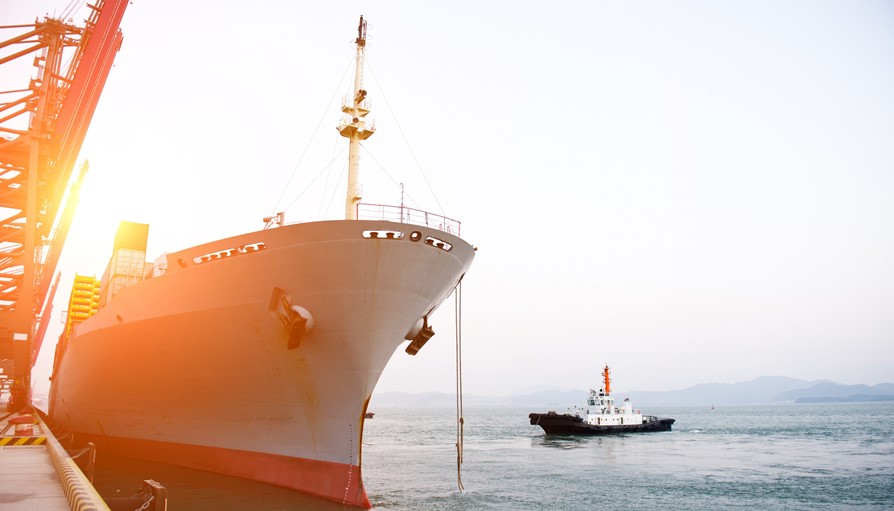
Polyester coatings provide excellent weather resistance. They increase durability with a high-gloss finish. They are also highly chemical resistant. Polyester coatings are often used in exterior applications where temperatures and weather conditions are constantly changing and chemical exposure is high, such as boats, vehicles, and aeroplanes.
Intumescent coatings
When exposed to extreme heat or open flames, these types of coatings can expand up to 100 times their original thickness and turn into foam-like layers. That insulate structures from fire. Because these coatings are able to maintain the integrity of different components in case of fire, they’re one of the best choices for high-heat applications.
Wrap up
No matter what surface you want to coat with industrial coating, knowing the insights is always important before starting the project. With the above information, you can choose the best type of commercial coating and get the desired outcome that meets your expectations.